Simplicity in the Kitchen
-
Simon Vinall
- Case Study
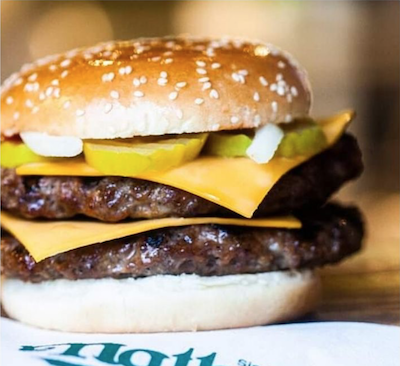
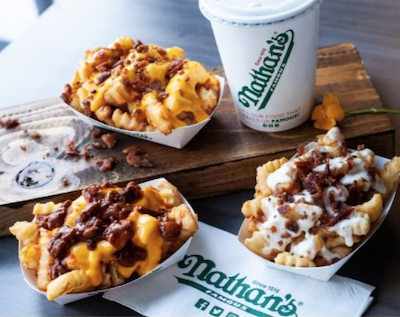
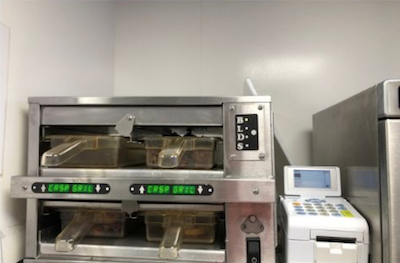
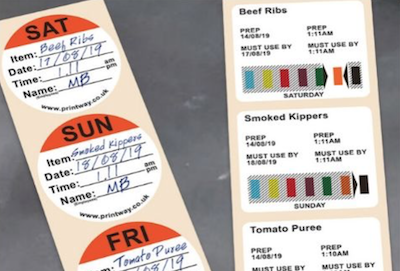
Nathan's Famous is a worldwide company founded in 1916 in Brooklyn, New York. The original. Nathan's Famous hot dog stand still operates daily in Coney Island. In 2019 Nathan's Famous opened two restaurants in the UK Located in Bournemouth and Southampton. The new restaurants have received great reviews and media attention and are planning to open more restaurants this year.
The menu consists of the world-famous hot dogs and fries, burgers, chicken sandwiches, tenders and wings, cheesesteaks, salads, expanded dessert items and beverages including a famous lemonade. To maintain high standards, operations director Amy Kavanagh needed to find a solution to ensure food safety and freshness in their busy kitchens to reduce incorrect labelling, spelling mistakes and time spent on handwritten labels.
To ensure food safety requirements, food labelling and rotation in the kitchen needs to be very accurate. To reduce human error and improve efficiency in both sites, operations director Amy decided to get in touch with a local food labelling solutions supplier Fresh Food Labels for advice.
Nathan's Famous solution was the SATO TH208 compact and light automated date labelling printer which ensures that standards are observed, leaving no possibility for interpretation. All food items on the system are pre-set with the correct product identification, preparation time and use-by date.
HOW NATHAN'S FAMOUS BENEFITED PROM SATO TH708
The right solution
- The system enabled the team to print accurate shelf life labels to ensure food safety
- The risk of error when handled by different staff has been significantly reduced - thanks to the ease of set-up and automation. The system enabled high-quality labelling and continuity of kitchen processes without compromise
- Reduced prep time with automated shelf life calculations
- Reduced health code violations and reduced spoilage caused by illegible handwriting
- Promoted labelling consistency across both sites
- Print nutrition, ingredient, food prep and delivery labels
- Retrieve nutritional values from the inbuilt product database
- Options to turn mobile with a battery kit
- Antimicrobial casing ensures easy cleaning
- Reduced staff training time
Before an automated food labelling solution was deployed, Nathan's Famous used dot labels that were costly and due to human error not always accurate. After an initial telephone conversation, Amy arranged a meeting with the Fresh Food Labels sales representative to discuss Nathan's Famous kitchens needs and available solutions.
The SATO TH208 labelling printer met all the criteria and shortly after these printers were installed in both Bournemouth and Southampton sites that helped to keep consistency across both sites. Labelling printers at both sites run two programs - one is being used for the food prep and another one to print delivery labels, so they do not to re-pack food for delivery orders.
A new solution is cheaper to run than purchasing day dot labels, it helped to reduce human error in the kitchen, is easy to use and it takes no time to train staff how to use a food labeller.
Simplicity in the Kitchen
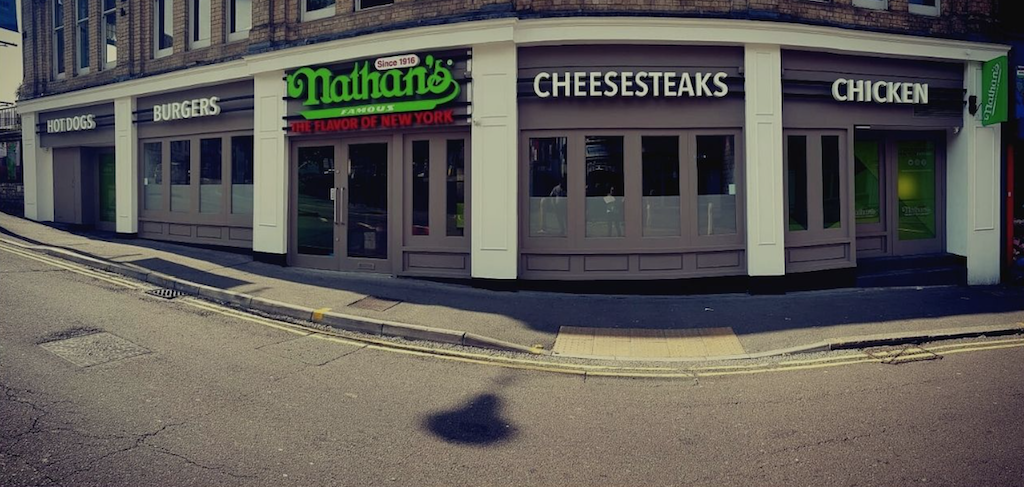
-
Simon Vinall
- Case Study
Nathan's Famous is a worldwide company founded in 1916 in Brooklyn, New York. The original. Nathan's Famous hot dog stand still operates daily in Coney Island. In 2019 Nathan's Famous opened two restaurants in the UK Located in Bournemouth and Southampton. The new restaurants have received great reviews and media attention and are planning to open more restaurants this year.
The menu consists of the world-famous hot dogs and fries, burgers, chicken sandwiches, tenders and wings, cheesesteaks, salads, expanded dessert items and beverages including a famous lemonade. To maintain high standards, operations director Amy Kavanagh needed to find a solution to ensure food safety and freshness in their busy kitchens to reduce incorrect labelling, spelling mistakes and time spent on handwritten labels.
To ensure food safety requirements, food labelling and rotation in the kitchen needs to be very accurate. To reduce human error and improve efficiency in both sites, operations director Amy decided to get in touch with a local food labelling solutions supplier Fresh Food Labels for advice.
Nathan's Famous solution was the SATO TH208 compact and light automated date labelling printer which ensures that standards are observed, leaving no possibility for interpretation. All food items on the system are pre-set with the correct product identification, preparation time and use-by date.
HOW NATHAN'S FAMOUS BENEFITED PROM SATO TH708
The right solution
- The system enabled the team to print accurate shelf life labels to ensure food safety
- The risk of error when handled by different staff has been significantly reduced - thanks to the ease of set-up and automation. The system enabled high-quality labelling and continuity of kitchen processes without compromise
- Reduced prep time with automated shelf life calculations
- Reduced health code violations and reduced spoilage caused by illegible handwriting
- Promoted labelling consistency across both sites
- Print nutrition, ingredient, food prep and delivery labels
- Retrieve nutritional values from the inbuilt product database
- Options to turn mobile with a battery kit
- Antimicrobial casing ensures easy cleaning
- Reduced staff training time
Before an automated food labelling solution was deployed, Nathan's Famous used dot labels that were costly and due to human error not always accurate. After an initial telephone conversation, Amy arranged a meeting with the Fresh Food Labels sales representative to discuss Nathan's Famous kitchens needs and available solutions.
The SATO TH208 labelling printer met all the criteria and shortly after these printers were installed in both Bournemouth and Southampton sites that helped to keep consistency across both sites. Labelling printers at both sites run two programs - one is being used for the food prep and another one to print delivery labels, so they do not to re-pack food for delivery orders.
A new solution is cheaper to run than purchasing day dot labels, it helped to reduce human error in the kitchen, is easy to use and it takes no time to train staff how to use a food labeller.